Types of Couplings and Their Applications
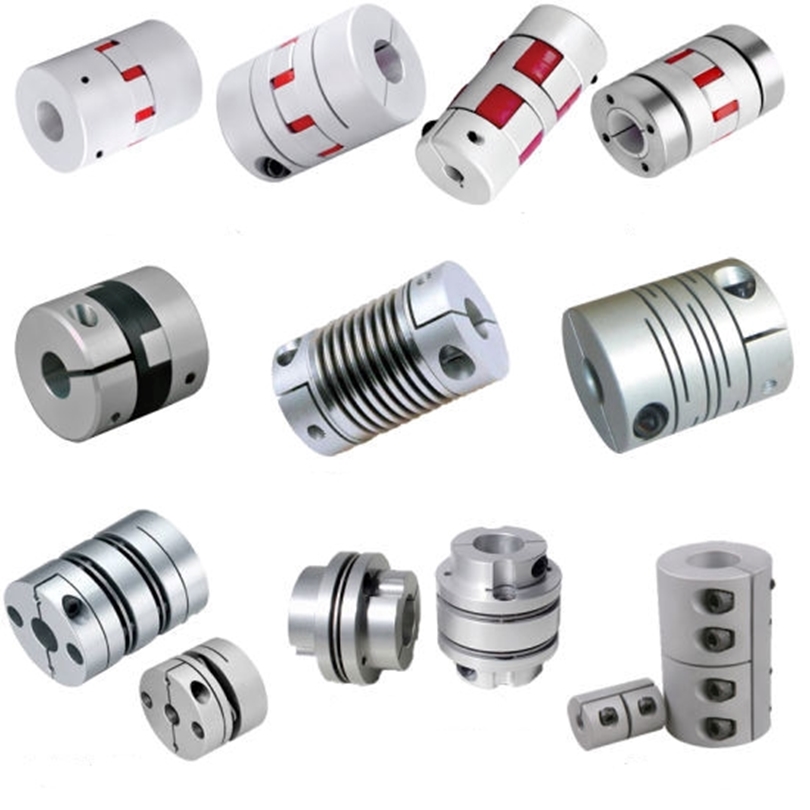
Beam Couplings
The beam coupling consists of single or multiple helical cuts in the coupling body which typically can accommodate parallel misalignments up to 0.025 inch and angular misalignments up to 7 degrees. They are used primarily for motion control applications where torques are typically below 100 inch-lbs. Zero backlash designs available ensure positioning accuracy between driving and driven shafts.
Bellows Couplings
Bellows couplings are also suited to motion control applications. They consist of multiple convolutions of metal which provide high torsional stiffness which is important to positioning applications. Torsional stiffness reduces the level of angular and parallel misalignment they can accommodate compared with beam couplings, although torque transmission capabilities are about similar.
Chain Couplings
Chain Couplings are suited to power transmission applications and are used to transmit power up into the hundreds of horsepower range. Angular and parallel misalignment allowances are typically 2 degrees and 0.015 inches, respectively. Typical chain couplings use special chain sprockets and double wide roller chains whose clearances permit the design to operate as a flexible coupling.
Jaw Couplings
Curved and Straight Jaw couplings are used for both motion control and light power transmission applications and consist of pairs of multi-jawed hubs that mate with elastomeric spiders. The design allows for backlash-free torque transmission. Accommodation for parallel misalignment usually approaches 0.01 inch and angular misalignment about 1 degree. Elastomeric spiders give these couplings some damping capacity and of often the spiders are available in different durometers to lend specific properties to the individual couplings. These couplings often operate without lubricant and can transmit torque up into the 1000 inch-lb. range.
Diaphragm Couplings
Diaphragm couplings are generally used for high power transmission such as found in turbomachinery. Typically they employ one or more flexible metal convoluted discs which transmit power to an inner spacer shaft then back out through another diaphragm stack to the driven machinery. A principal advantage over gear type couplings is their lack of lubrication requirements. Diaphragm couplings are capable of high torque transmission and high-speed operation.
Disc Couplings
Disc couplings use single or multiple discs and single or double stages which bolt to the shaft hubs. They are used for power transmission and rely on the flexibility of their thin metal discs to transmit torque and accommodate angular misalignment. They are not especially good at managing parallel misalignment. They are capable of transmitting high torques and are often used to couple high horsepower motors, gas turbines, etc. to loads.
Gear Couplings
Gear couplings also transmit high torques. They have misalignment capabilities generally about 0.01-0.02 inch in parallel and 2 degrees in angular. Gear couplings are often used in pairs with spacer shafts to span the distance between the driving and driven equipment. They generally require lubricant although some designs intended for lighter duty use lubricant free nylons or other polymers for the center sleeve.
Grid Couplings
Grid couplings employ spring-like connecting elements that weave between slots machined in the coupling hubs. They are capable of high torque transmission with an added bonus of shock absorption and torsional vibration dampening. They operate without lubricant. They are appropriate for power transmission and capable of handling parallel misalignment up to 0.30 inch and angular misalignment of about ¼ degree.
Oldham Couplings
Oldham couplings handle high degrees of parallel misalignment owing to their sliding element design. Use of an elastomer center element instead of metal is popular in modern versions. Some manufacturers claim an ability to tolerate up to 5-degree angular misalignment through the use of cylindrical, rather than rectangular, sliders.
Schmidt Couplings
Schmidt couplings are designed specifically to operate on shafts that are offset. They aren’t flexible couplings in the strictest sense, which are designed to accommodate slight misalignment in shafts that are theoretically parallel and square to one another. Schmidt couplings are used in papermaking, printing, and similar machines and function more like a 1:1 gearbox in a more compact space.
Clamping Couplings
Rigid one- and two-piece Clamping couplings lack accommodation for shaft misalignment and are popular for slow or intermittent shafting arrangements where alignment is not of concern. They are the simplest form of shaft coupling and apart from their lack of misalignment tolerance, are inexpensive zero-backlash devices.
Other Couplings
Coupling designs are many only the principal ones are detailed above. Other coupling types include meshing tooth, or Hines, designs, pin and bush couplings, and spline couplings.